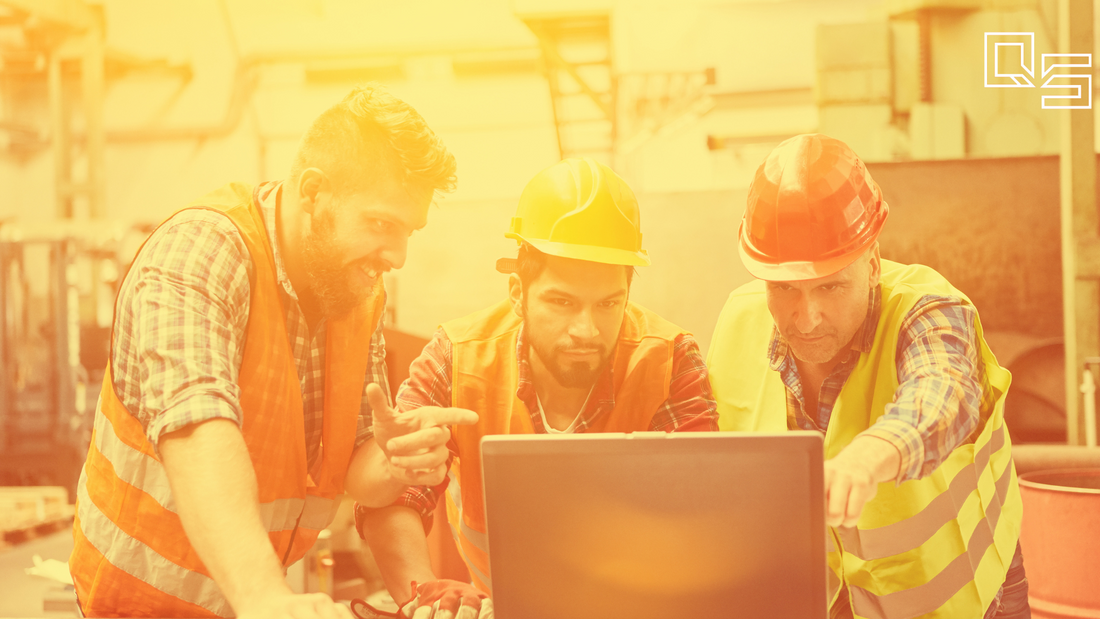
5 Common Mistakes in Cost-Benefit Analysis for Construction Businesses (And How to Avoid Them)
Construction project planning is a crucial step in every build. Given the significant investments and high-stakes decision-making in construction, budget is often a critical part of planning.
One of the most important components in planning is the cost-benefit analysis. It is already a given that most projects have tight margins and deadlines to deal with; therefore, selecting the right strategies that would reap more rewards is an essential part of every project.
What is cost-benefit analysis?
Cost-Benefit Analysis or CBA is a process of determining whether the costs of a project and its determined benefits are feasible. Simply put, through CBA, stakeholders of the project can determine whether the project is worthwhile by summing up its rewards against their investments.
It is important to note that CBA does not only include tangible materials in its analysis. It also involves less concrete factors.
Because of its value to the project, many construction teams do not miss out on performing a CBA. However, there are common mistakes when doing a CBA that run the risk of creating havoc in the project’s budget.
Here are common mistakes in Cost-Benefit Analysis and how to avoid them during construction project planning.
1. Overlooking Intangible Benefits
As mentioned earlier, CBA does not only take account of concrete numbers, but also of intangible factors. Unfortunately, many business owners and project managers focus mostly on things that are easier to see, such as cost savings and profits, while completely neglecting benefits like sustainable practices, team safety, and even staff morale.
Because of this mistake, many business owners and project managers miss out on future cost savings and market opportunities, which could help improve the project outcomes and even significantly grow the business.
How to avoid it: The best way to avoid overlooking intangible benefits is to include lifecycle cost analysis (LCCA) in your CBA. Businesses could also hire business consultants to better quantify benefits such as reduced operating costs, tax incentives, and market differentiation.
2. Underestimating Site-Specific Costs
Have you ever underestimated a site's hidden costs? You're not alone. Many teams skip thorough assessments, and it costs them.
Site conditions often come with their own set of challenges and requirements. Factors such as soil quality, local regulations, and even logistical challenges can run up project costs.
However, the reality is that site conditions often get overlooked due to time constraints, wrong assumptions, and lack of communication. As a result, the project suffers from budget overruns and unforeseen delays.
How to avoid it: The best way to avoid this mistake is to conduct thorough assessments early on. Dedicate enough time to properly assess the site conditions and clearly communicate with all the stakeholders involved. Experienced professionals can also significantly help in this process by properly anticipating location-specific changes.
3. Overlooking Risks in Supply Chain and Labour
The construction industry often experiences a lot of changes in a short span of time. Because of the dynamic nature of the industry, material shortages, labour strikes, and fluctuating prices often cause budget nightmares in a lot of construction project planning and execution.
Furthermore, a lot of construction businesses lack an integrated risk management process. Because of the oversight in addressing risks, projects often experience increased costs, delays, and worse—strained client relationships. In common cases, the pressure to keep costs low in order to win the bid leads to this mistake.
How to avoid it: Factoring supply chain and labour risks during the analysis is still the best way to avoid this mistake. As you and your team plan projects, always include contingencies in your budget and have a list of reliable backup suppliers in your directory as well.
4. Using Outdated Market Data
As we know, the construction industry is a dynamic one, with many interrelated factors—from labour laws and building regulations to market changes. However, a lot of construction professionals still tend to rely on old cost data for materials, equipment, and labour rates. The problem of using outdated market data could be chalked up to the overconfidence of many experienced project managers and contractors or just plain time constraints.
As a result, the project’s feasibility and profitability can be misjudged, and you would have to deal with a faulty analysis.
How to avoid it: The best way to avoid this mistake is to maintain an up-to-date database of costs and market trends. It may be tedious, but it will save you from a lot of headaches (and heartaches) in the future. You can also consult industry and local market experts regularly through platforms like Construction Enquirer and joining professional networks such as the Federation of Master Builders.
5. Poor Presentation of CBA Findings to Stakeholders
Let’s face it—it takes a special skill to clearly communicate overly technical data to clients and stakeholders. For many of us, we tend to think that our clients speak the same language as we do and might not understand the value of our CBA findings.
Because of the poor presentation of the CBA findings, clients might end up perceiving the project as risky despite solid data. You might also lose a lot of business opportunities in the process.
How to avoid it: Highlight the bottom line: why this project or strategy benefits the client or business. For a lot of clients, this is ultimately what matters most. In addition, you can also simplify large data by using visuals like charts and graphs.
So there you have it, the five common mistakes you should avoid when making your CBA.
Because of the high stakes in construction, a precise, well-executed cost-benefit analysis can significantly improve your project outcomes. Using tools and construction software can help you and your team speed up the process and create a more accurate analysis.
When was the last time you audited your CBA process? This is your sign to update and adopt these strategies for your next construction project planning session.